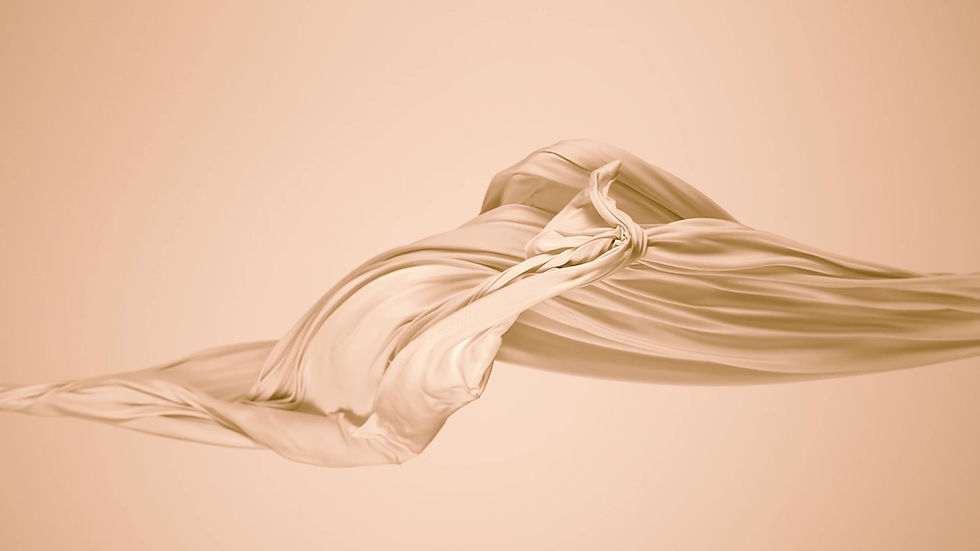
Additive Manufacturing
Additive manufacturing (AM) is a technology that describes the way 3D objects can be built. The term “3D Printing” is commonly the technology that comes to mind, but 3D Printing is actually categorized under one of the 7 main AM processes. The AM equipment reads data from sketches made in Computer-Aided Design (CAD) software, then uses that information to lay down material in successive layers to create a piece. The 7 main AM processes are Binder Jetting, Directed Energy Deposition, Material Extrusion, Material Jetting, Powder Bed Fusion, Sheet Lamination, and Vat Photopolymerization.
​
Currently, AM is being used to model a variety of things, like medical implants, automobiles, and fashion products [1]. Some of the benefits include assemblies can be printed in one process, support material and powder can often be recycled back into the system, and the emissions from transport are reduced due to the ability to manufacture products near consumers or even at home.

01
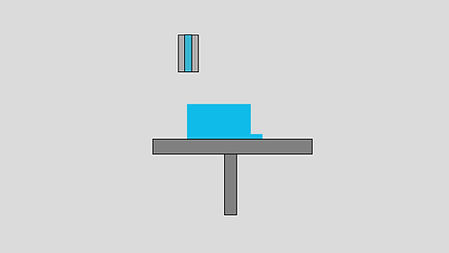
Material Extrusion
Material Extrusion is the generic term for all additive manufacturing processes in which material is dispensed through a nozzle to form shapes [2]. The nozzle is attatched to a print head, which moves along the x-y-z axis. The print head moves up in the z-direction after each layer of material is extruded and stops when the build is complete. This process is also called Fused Deposition Modeling (FDM) [2].
​
Printing Process
-
The nozzle attached to the printhead deposits material directly onto the build platform.
-
The following layers are added on top of the previous layers. The printhead moves up and the build platform remains stationary.
-
The layers are melted together upon deposition.
Post-Printing Process
Once the material is extruded, the layers are exposed to the ambient air and harden. There are not additional material used to cure a build.
​
Materials
Materials include polymers and plastics. An example of polymer is Polycarbonate (PC). Thermoplastics are the most popular material for material extrusion. Examples of thermoplastics are Acrylonitrile Butadiene Styrene (ABS), PolyLactic Acid (PLA), High-Impact Polystyrene (HIPS), Thermoplastic PolyUrethane (TPU), aliphatic PolyAmides (PA, also known as Nylon), PolyEther Ether Ketone (PEEK), and PolyEtherimide (PEI) [3].
​
Equipment Used Today
Applications
The material extrusion process is applicable to many fields. Buildings can be constructed with concrete extrusion machines [2]. Human tissues and organs have been extruded using this technique [2].
Advantages and Disadvantages
Advantages:
-
Widespread process [1]
-
Lower cost machines make this process available to a wide audience [1]
-
ABS plastic is a common, easily accessible material that has good structural properties
Disadvantages:
-
The nozzle radius limits and reduces the final quality [1]
-
The accuracy and speed are low when compared to other processes [1]
-
The accuracy of the final model is limited to material nozzle thickness [1]
-
The constant pressure of material is required in order to increase the quality of finish [1]
​
​
​
​
​
​
​
​
​
​
​
​
​
​
​
​
GrafEngin. (2016). material extrusion. Available at: https://www.youtube.com/watch?v=VQR_Q8_KhCs. (12/9/23).
​
References
[1] https://www.lboro.ac.uk/research/amrg/about/the7categoriesofadditivemanufacturing/materialextrusion/
[2] https://all3dp.com/2/main-types-additive-manufacturing/
[3] https://make.3dexperience.3ds.com/processes/material-extrusion
02
Material Jetting
Material jetting is a process that combines 2D inkjet printing and stereolithography (SLA). The material, a photoreactive resin, is heated to obtain the needed viscosity for printing. Then, the print head moves horizontally and shoots hundreds of micro-droplets of material onto the build platform [1]. This can be continuous or drop by drop process [1]. These droplets form a layer that is solidified by cooling, UV-light curing, or by evaporating the liquid part of the material via an infrared laser [1]. The build platform lowers as more material is deposited.

​
Printing Process
-
The print head is positioned above the build platform. Material is deposited in droplets from the print head onto the surface.
-
The droplets of material solidify, and this repeats until the model is complete.
-
When the model is complete, the layers are cured by UV light.
Post-Printing Process
In the liquid resins, there are UV photo-curable resins. The curing process is completed using UV rays. One of the most common build material for material jetting is polymers in the form of liquid resins [3]. This is due to the advantage of using the UV photo-curable resins that do not need extra post-processing steps [3].
​
Materials
Materials include polymers in the form of liquid resins, plastics, and metal [1]. Polymers include polypropylene, HDPE, PS, PMMA, PC, ABS, HIPS, EDP [2].
​
Equipment Used Today
-
Object500 Connex3
-
Jet Fusion 4200
Applications
Material jetting 3D printing technology has applications in making realistic prototypes. The process provides an excellent level of detail, high accuracy, and a smooth surface finish [3]. Material jetting allows a designer to print a design in multiple colors and with a number of materials in a single print. [3]
Advantages and Disadvantages
Advantages:
-
Each printhead can store a different colored material, allowing multi-material and multi-color parts to be used simultaneously [1]
-
Very high accuracy [1]
-
Smooth finishes [1]
-
Low waste due to the deposition of droplets [2]
Disadvantages:
-
High equipment cost [1]
-
Support material is often required [2]
-
UV activated photopolymers lose mechanical properties over time and can become brittle [3]
​
​
​
​
​
​
​
GrafEngin. (2016). material jetting. Available at: https://www.youtube.com/watch?v=m8n6FBKgY2g. (12/9/23).
​
References
[1] https://all3dp.com/2/main-types-additive-manufacturing/
[2] https://www.lboro.ac.uk/research/amrg/about/the7categoriesofadditivemanufacturing/materialjetting/
[3] https://make.3dexperience.3ds.com/processes/material-jetting
03
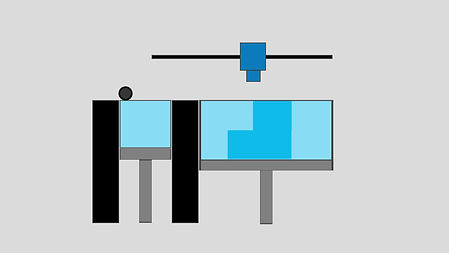
Binder Jetting
Binder Jetting uses two materials. The two materials are a powder base for its build material and a liquid binder agent. The manufacturing process starts with a leveling roller that spreads a thin layer of the powder material over the build platform [1]. Then the printhead moves horizontally while spraying the binder agent on the specified area of the powder layer.
The binder agent acts as an adhesive between the powder layers. This is due to the chemical reaction the liquid binder creates. The build platform lowers as subsequent layers are added until the piece is finished. The curing process will be highlighted in the following.
​
Printing Process
-
The nozzle attached to the printhead deposits material directly onto the build platform.
-
The following layers are added on top of the previous layers. The printhead moves up and the build platform remains stationary.
-
The layers are melted together upon deposition.
Post-Printing Process
Once the material is extruded, the layers are exposed to the ambient air and harden. There are not additional material used to cure a build.
​
Materials
Materials include polymers and plastics. An example of polymer is Polycarbonate (PC). Thermoplastics are the most popular material for material extrusion. Examples of thermoplastics are Acrylonitrile Butadiene Styrene (ABS), PolyLactic Acid (PLA), High-Impact Polystyrene (HIPS), Thermoplastic PolyUrethane (TPU), aliphatic PolyAmides (PA, also known as Nylon), PolyEther Ether Ketone (PEEK), and PolyEtherimide (PEI) [3].
​
Equipment Used Today
Applications
The material extrusion process is applicable to many fields. Buildings can be constructed with concrete extrusion machines [2]. Human tissues and organs have been extruded using this technique [2].
Advantages and Disadvantages
Advantages:
-
Widespread process [1]
-
Lower cost machines make this process available to a wide audience [1]
-
ABS plastic is a common, easily accessible material that has good structural properties
Disadvantages:
-
The nozzle radius limits and reduces the final quality [1]
-
The accuracy and speed are low when compared to other processes [1]
-
The accuracy of the final model is limited to material nozzle thickness [1]
-
The constant pressure of material is required in order to increase the quality of finish [1]
​
​
​
​
​
​
​
​
​
​
​
​
​
​
​
​
Proxima 3D. (2016). Binder Jetting 3D Printing Process. Available at: https://www.youtube.com/watch?v=97doBH9jSXY. (12/9/23).
​
References
[1] https://www.lboro.ac.uk/research/amrg/about/the7categoriesofadditivemanufacturing/materialextrusion/
[2] https://all3dp.com/2/main-types-additive-manufacturing/
[3] https://make.3dexperience.3ds.com/processes/material-extrusion
04
Directed Energy Deposition
Directed Energy Deposition (DED) creates pieces by directly melting materials and deposing them on the piece in a layer by layer process. When the material is pushed through the nozzle, energy is focused on the flow, and the material is melted and deposited at the same time [2]. The focused energy source is usually a laser or electron beam, and the energy cource is mounted with a nozzle [2]. Once that layer is solidified, the process repeats until the piece is finished. This process is similar to material extrusion, but it requires more energy and the material can be deposited in several directions [2]. Laser engineered net shaping (LENS), directed light fabrication (DLF), direct metal deposition (DMD), Laser Deposition Welding (LDW), and 3D laser cladding are also process that fall under DED [2, 3].

Printing Process
-
An arm with a nozzle moves over the build platform.
-
Material (wire or powder form) is deposited from the nozzle onto the existing surfaces.
-
The material is melted using an energy source. These sources can be a a laser, electron beam, or plasma arc.
-
The model is built up layer by layer [1].
Post-Printing Process
There is no additional process for curing after the piece is made. Post-processing steps may occur only if a certain finish is requested.
Materials
This additive manufacturing technique is mostly used with plastic, metal, ceramic [2].
Equipment Used Today
-
Lasertec 65
-
Integrex-i-400 AM
Applications
Parts can be built from scratch, and DED can also be used to fix complex damaged parts, such as turbine blades or propellers [3].
Advantages and Disadvantages
Advantages:
-
The ability to control the grain structure to a high degree allows high-quality repairs [1]
-
DED pieces can display mechanical properties comparable to (or better than) those of cast or wrought metals [2]
-
The nature of the DED process doesn’t require gravity, making it a potential process for applications in space [2]
-
LENS process can repair damaged parts that traditional methods can’t otherwise fix [2]
Disadvantages:
-
Finishes can vary depending on paper or plastic material but may require post-processing to achieve the desired effect [1]
-
High equipment cost [2]
-
The speed can often be sacrificed for high accuracy and a pre-determined microstructure [1]
-
Most DED 3D printers are industrial machines with very large footprints that require a closed and controlled environment to operate [3]
​
​
​
​
​
​
​
​
​
​
​
​
​
​
Stratasys Direct Manufacturing. (2019). How it Works: Direct Metal Laser Sintering (DMLS). Available at: https://www.youtube.com/watch?v=yiUUZxp7bLQ&feature=emb_title. (12/8/23).
​
References
[1] https://all3dp.com/2/main-types-additive-manufacturing/
[2] https://make.3dexperience.3ds.com/processes/powder-bed-fusion
[3] https://www.lboro.ac.uk/research/amrg/about/the7categoriesofadditivemanufacturing/powderbedfusion/
05

Powder Bed Fusion
Powder Bed Fusion is a process that occurs in a near-vacuum chamber with an inert gas [1]. The chamber is heated and the process starts by spreading a thin layer of powder material onto a build platform [1]. A thermal energy source, usually a laser, searches regions of the bed that will be used to bond the powder together, and this forms a thin layer of combined material [1]. Once a layer is complete, the build platform lowers and another layer of powder is spread on top. The layers are fused together, and when the process is complete, the unbound powder is removed from the part [1].
There are several Powder Bed Fusion methods. These methods include Selective Laser Sintering (SLS), Selective Laser Melting (SLM) or Direct Metal Laser Sintering (DMLS), Electron Beam Melting (EBM), and Multi Jet Fusion (MJF) by HP [2].
​
Printing Process
-
A layer of material is spread over the build platform and then a laser fuses the first later.
-
A roller spreads a new layer of powder across the previous.
-
The preceding layers are fused and the process repeats until the model is created.
-
The loose, unfused powder remains in the build bed, but it is removed during post-processing.
Post-Printing Process
There are no additional curing processes that the model undergoes before post-processing.
​
Materials
Materials include plastics, metals, and ceramics. Nylon is one of the plastics used in this process. Metals include Stainless Steel, Titanium, Aluminium, Cobalt Chrome [1].
Equipment Used Today
-
SLM 280
-
Arcam Spectra L
-
Formiga P110
Applications
Powder bed fusion is used for production parts. The mechanical properties of metal parts produced by SLM and EBM methods are similar to machining and casting [1]. The medical and aerospace industries are already making use of these technologies [1]. In the aerospace industry, the new Boeing 777X engines contain around 300 additively-manufactured components each, and all of them are made by powder bed fusion methods [1].
Advantages and Disadvantages
Advantages:
-
Unused material can sometimes be recycled [1]
-
Suitable for visual models and prototypes [2]
-
The powder acts as an integrated support structure [2]
Disadvantages:
-
Lack of structural properties in materials [2]
-
Size of models are limited to the powder bed size
-
Costly material and post-processing steps [1]
​
​
​
​
​
​
​
​
​
​
​
​
​
​
Stratasys Direct Manufacturing. (2019). How it Works: Direct Metal Laser Sintering (DMLS). Available at: https://www.youtube.com/watch?v=yiUUZxp7bLQ&feature=emb_title. (12/8/23).
​
References
[1] https://all3dp.com/2/main-types-additive-manufacturing/
[2] https://make.3dexperience.3ds.com/processes/powder-bed-fusion
[3] https://www.lboro.ac.uk/research/amrg/about/the7categoriesofadditivemanufacturing/powderbedfusion/
​
​
06
Vat Photopolymerization
Vat photopolymerization, also known as stereolithography (SLA), is the process by which a liquid is cured by a light source, turning it into a solid [1]. This phenomenon became known as polymerization and was the very first industrial additive manufacturing technology [1]. A laser draws the shape of each layer into a resin-filled vat, and once it solidifies, the build platform moves to make room for the next layers. During this process, fresh resin fills the gaps.

​
Printing Process
-
The build platform lowers down into the resin vat by the layer thickness.
-
UV light is used to cure the resin layer by layer. The platform moves downwards as additional layers are built on top of the existing layers.
-
In some machines, a blade moves between layers to provide a smooth resin base to build the next layer on.
-
The model is removed after the vat is drained of resin.
Post-Printing Process
Once the model is complete, it cures in a special chamber with additional UV light [1]. When the resin is fully cured, the model is ready for use.
​
Materials
This process uses photocurable liquid resins and polymers.
​
Equipment Used Today
-
ProX 800
-
Form3
Applications
Vat photopolymerization is used in several markets because the materials are easily accessible [1]. The method is useful for making various consumer products, like hearing aids. The manufacturer Sonova uses SLA in the production of hearing aids to create products customized to individual clients [1]. Another industry is the shoe industry; Adidas and Nike use this technology for serial production [1].
Advantages and Disadvantages
Advantages:
-
High level of accuracy [1]
-
Smooth finishes [2]
-
Faster printing time
-
While many additive manufacturing processes need to trace the part pattern on each layer, Vat Polymerization can print by projecting the entire layer pattern on the liquid surface [3]
-
Models might be used more for quick displays or views of a newly modeled part [3]
Disadvantages:
-
Support structures often required [1]
-
Lengthy post-processing [1]
-
Models are still not as good in terms of impact strength and lasting durability, especially when compared to injection molded parts [3]
​
​
Dassault Systèmes. (2022) What is Photopolymerization (SLA, DLP, CDLP)? Available at: https://www.youtube.com/watch?v=2zvxjzC6prk. (12/8/23)
​
References
[1] https://all3dp.com/2/main-types-additive-manufacturing/
[2] https://www.lboro.ac.uk/research/amrg/about/the7categoriesofadditivemanufacturing/materialjetting/
[3] https://make.3dexperience.3ds.com/processes/material-jetting
07
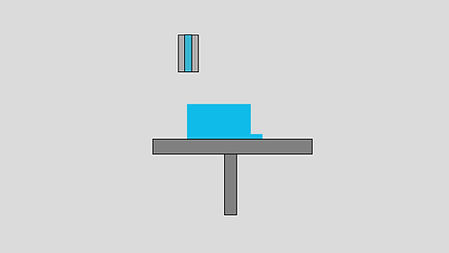
Sheet Lamination
There are two main methods in Sheet Lamination. The first method is Ultrasonic Addition Manufacturing (UAM). In this method, room-temperature metal sheets are bonded together by the application of ultrasonic waves and mechanical pressure [1]. Then, the sheets are sliced using a laser or by milling before or after the metal is bonded. This produces each layer that will be stacked together to create a 3D model. The parts can be polished before or after this slicing process to achieve a finish.
The second method is Laminated Object Manufacturing (LOM). In this method, the paper sheets are heated by a roller that also presses them against the build plate to improve the adhesion [1]. The surrounding boundaries of the part are usually created with cross-hatching to provide easier extraction when the process is finished [1]. A subprocess, Selective Deposition Lamination (SDL), uses colored printed sheets of paper to create full-color 3D objects.
​
Printing Process
-
The material is positioned in place on the build bed.
-
The material is bonded in place using adhesive on the previous layer.
-
A laser cuts the required shape from the layer.
-
Steps two and three can be reversed. The material can be cut then bonded onto the previous layer. This process repeats until the model is complete.
Post-Printing Process
Once the model is taken out of the surrounding material, is extruded, the layers are exposed to the ambient air and harden. There is no additional material used to cure a build.
​
Materials
This process uses metals, like aluminum, copper, stainless steel, and titanium alloys, and paper. Metals are most suitable for UAM, papers are most suitable for LOM, and it is also possible to use plastic [1].
Equipment Used Today
-
CG-1 Full-Colour
-
SonicLayer 1200
Applications
UAM provides a reliable way to join dissimilar metals, and it is ideal for creating new material combinations [1]. LOM is usually used for rapid prototyping since it can’t produce parts with complex geometries, which lack dimensional accuracy [1]. SDL might be a cost-effective option for full-color prototyping.
Advantages and Disadvantages
Advantages:
-
UAM requires low levels of energy since the metal sheets aren’t melted [1]
-
LOM uses cheap materials that are very easy to handle [1]
-
Ability to integrate as hybrid manufacturing systems [2]
-
Full color prints – LOM/SDL can print in the whole color spectrum [2]
-
Both techniques are also relatively fast [1]
Disadvantages:
-
Low part strength in LOM [1]
-
Lengthy post-processing UAM [1]
-
Hollow parts (internal voids and cavities) are difficult to produce in some types of sheet lamination processes [2]
-
Material waste can also be high if the part being made is smaller than the build area or the sheet size [2]
-
Finishes can vary depending on paper or plastic material but may require post-processing to achieve the desired effect [3]
​
​
​
​
​
​
​
​
​
​
​
​
​
​
​
GrafEngin. (2016). sheet lamination. Available at: https://www.youtube.com/watch?v=ciCxNgROtm4. (12/8/23).
​
References
[1] https://all3dp.com/2/main-types-additive-manufacturing/
[2] https://engineeringproductdesign.com/knowledge-base/sheet-lamination/
[3] https://www.lboro.ac.uk/research/amrg/about/the7categoriesofadditivemanufacturing/sheetlamination/